HPI (High Performance Industrietechnik GmbH), mit Hauptsitz in Ranshofen, Österreich, entwickelt, konstruiert, fertigt und liefert schlüsselfertige Systeme für die Leichtmetallindustrie. Metallurgische Hersteller verwenden typischerweise Leichtmetalle, wie Aluminium und Magnesium, um Produkte aus Leichtlegierungen herzustellen.
Für einen der metallurgischen Kunden hat HPI ein automatisiertes Leitfähigkeitsmesssystem für die zerstörungsfreie Materialprüfung konzipiert und entwickelt. Das von HPI gebaute Leitfähigkeitsmesssystem integriert unser NORTEC 600 Wirbelstrom-Prüfgerät zu Mess- und Prüfzwecken zur Einhaltung von Qualitätsanforderungen.
Die Herausforderung: Ein System, das die Leitfähigkeit bei Produktionsgeschwindigkeit validiert
Gemäß einem Artikel aus der Zeitschrift Aluminium Times hat HPI das System entwickelt, um Leitfähigkeitstests zur Beurteilung des Wärmebehandlungszustands von Aluminiumbleche durchzuführen. Diese Bleche sind bis zu 4.200 mm breit, bis zu 33.000 mm lang und zwischen 1 mm bis 210 mm (~0,039 Zoll bis 8,3 Zoll) dick. dick. Diese Bleche werden zu Halbzeugen aus Aluminium- und Magnesiumlegierungen verarbeitet, die an die Luftfahrtindustrie geliefert werden.
Das metallurgische Unternehmen benötigte das System für seinen neuen Walzwerkkomplex bestehend aus Kaltwalzwerk, Warmwalzwerk und Wärmebehandlung von Blechen. Der Herstellungsprozess erforderte eine integrierte zuverlässige ZfP-Prüflösung, die die Produktivität steigert und gleichzeitig die Materialien nach international anerkannten Normen validieren würde.
Die Herausforderung für HPI bestand darin, ein System zu entwickeln, das eine Hochgeschwindigkeitsmessung der Leitfähigkeit von Aluminiumblechen ermöglicht und gleichzeitig eine einheitliche Prüfleistung beibehält.
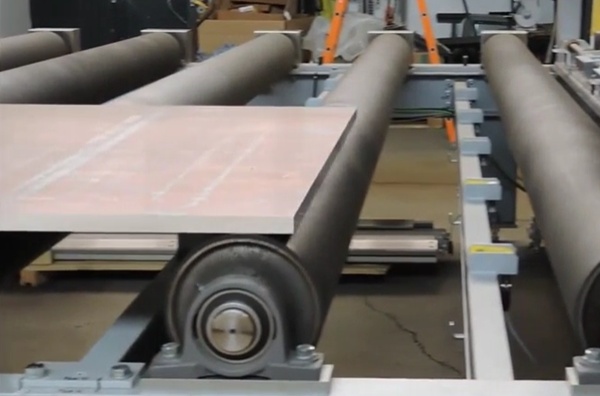
Ein großes Aluminiumblech wird auf einem Walzengang einer Produktionsstraße transportiert
Gründe für die Messung der Leitfähigkeit von Metallen
Anhand der elektrische Leitfähigkeitsmessung wird ermittelt, wie gut die Leitfähigkeit eines Materials ist, d. h., wie gut ein Material elektrischen Strom leiten kann. Solche Prüfungen ermöglichen, Informationen über die Zusammensetzung eines Materials zu erfassen. Anhand dieser Daten kann festgestellt werden, ob das Material für den vorgesehenen Verwendungszweck geeignet ist.
Viele Branchen integrieren Leitfähigkeitstests in ihre Qualitätskontroll- und Herstellungsprozesse, um die Authentizität der strukturellen Integrität des Metalls zu bestätigen und so festzustellen, ob die gewünschte Haltbarkeit und Leistung des Endprodukts erreicht wird.
Die Leitfähigkeit von Aluminium, das beim Bau von Flugzeugen verwendet wird, muss gemessen werden, um seine Entladungskapazität zu kennen und sicherzustellen, dass das Aluminium Materialbelastungen durch Ereignisse, wie Blitzeinschläge, standhält. Durch die Erkennung von Abweichungen in der Härte der Legierung kann mit der Leitfähigkeitsprüfung bestätigt werden, dass das Material ggf. durch die Wärmebehandlung beschädigt wurde, wodurch es spröder wird.
Vor- und Nachteile und typische Mängel von Aluminium
Aluminium hat eine geringere Dichte als andere gewöhnliche Metalle. Die Dichte von Stahl ist beispielsweise ein Drittel höher als die von Aluminium. Aufgrund des geringen Gewichts und der Festigkeit eignet sich Aluminium für den Flugzeugbau. Laut einiger Quellen wird ein modernes Flugzeug auf einen Aluminiumgehalt zwischen 75–80 % geschätzt. Da sie hauptsächlich aus Aluminium bestehen, können Flugzeuge mehr Gewicht tragen und sind treibstoffeffizienter.
Ein weiterer großer Vorteil von Aluminiumlegierungen ist ihre Korrosionsbeständigkeit, die die Haltbarkeit eines Flugzeugs erhöht. Flugzeuge sind ständig Naturgewalten und klimatischen Extremen ausgesetzt, von Temperaturen unter dem Gefrierpunkt in großen Höhen bis hin zu Niederschlägen, einschließlich Schnee und Regenstürmen. Obwohl Aluminium eine hohe Korrosionsbeständigkeit aufweist, ist es ein chemisch aktives Metall, sodass Korrosion auftreten kann.
Aluminiumkomponenten sind anfällig für verschiedene Arten von Korrosion, darunter:
- Lochfraß an der Oberfläche
- Intergranulare Korrosion
- Schichtkorrosion
- Spannungsrisskorrosion
- Ermüdungsrisse
- Reibverschleiß
Herstellungsprozesse wie maschinelle Bearbeitung, Umformung, Schweißen oder Wärmebehandlung können Spannungen in Aluminiumblechen (und damit Flugzeugteilen) hinterlassen. Diese Spannung kann in einer korrosiven Umgebung zu Rissbildung führen, wenn die Schwelle für Spannungskorrosion überschritten wird.
Vorteile von Wirbelstrom bei der ZfP für Luft- und Raumfahrtanwendungen
Mit der Wirbelstromtechnik werden metallische Werkstoffe ohne direkten Kontakt zerstörungsfrei geprüft. Sie wird häufig in der Luft- und Raumfahrtindustrie sowie in anderen Fertigungs- und Serviceumgebungen eingesetzt, in denen dünnes Metall auf potenzielle sicherheits- oder qualitätsbezogene Probleme untersucht werden muss.
Da die Wirbelstromprüfung eine elektromagnetische Ankopplung verwendet und kein direkter Kontakt mit dem Prüfteil bestehen muss, ist kein Koppelmittel erforderlich.
Die Wirbelstromprüfung kann für folgende Prüfungen verwendet werden:
- Oberflächenprüfung
- Prüfung unter der Oberfläche (normalerweise 3–4 mm)
Vorteile der Wirbelstromtechnologie:
- Prüfung durch Anstrichmittel und Beschichtungen (keine Lackentfernung erforderlich)
- Minimale Oberflächenvorbereitung (kann durch Schmutz prüfen)
- Einfache Bedienung nach nur minimaler Einarbeitung
- Liefert schnelle Ergebnisse und eignet sich daher für die Hochgeschwindigkeitsprüfung und die Prüfung großer Teile
- Geeignet für alle Materialien, die Strom leiten, einschließlich der in Flugzeugen üblichen Metalle wie Aluminium, Edelstahl und Stahl
Funktionsweise von Wirbelstromprüfgeräten

(a) Durch eine Spule geleiteter Wechselstrom erzeugt ein Magnetfeld (blau dargestellt). (b) Nähert man die Spule einem Strom leitenden Material, entsteht in diesem Material ein Wirbelstrom. (c) Fehler im Prüfteil stören den Pfad des Wirbelstroms. Diese Störung kann von dem Gerät gemessen werden.
Wenn elektrischer Wechselstrom durch eine oder mehrere Spulen einer Wirbelstromsonde fließt und sich diese Sonde nah an einem Prüfteil aus leitfähigem Material befindet, wird ein magnetisches Wechselfeld erzeugt, das Wirbelströme in dem Prüfteil induziert. Dieses Magnetfeld erzeugt einen Ankopplungseffekt.
Diskontinuitäten oder Abweichungen der Merkmale im Prüfteil verändern den Pfad des Wirbelstroms, was sich auf die induktive Betriebsreaktanz der Sonde auswirkt. Abweichungen der Materialdicke oder Fehler, wie Risse und Korrosion am Prüfteil werden von der Sonde erkannt. Diese Änderungen werden auf dem Bildschirm des Geräts in Phase und Amplitude des Signals widergespiegelt, die der Prüfer dann interpretiert.
HPIs Lösung zur Leitfähigkeitsmessung von Aluminiumblechen
Dieses Video zeigt die Lösung von HPI, ein automatisiertes System zur Hochgeschwindigkeitsmessung der Leitfähigkeit von Aluminiumblechen. Es ist zu sehen wie das NORTEC 600 Gerät in das HPI System auf einem Scanner integriert ist, der die Wirbelstromsonde schnell über die Kalibrierstation und über die Aluminiumbleche bewegt, nachdem sie auf Walzen in die Messstation geführt wurden.
Die Messprogramme können für jedes Blech vordefiniert werden, wobei die international anerkannten Standards und Normen ASTME 1004-02, MIL STD1537C, EN 2004-1 und AMS 2772F sowie die kundenspezifischen Prüfvorschriften der Luft- und Raumfahrtindustrie als Referenz dienen.

Leitfähigkeitsmesssystem für Aluminiumbleche mit integriertem NORTEC 600 Wirbelstromprüfgerät
HPI hatte früher manuelle Geräte für diese Art von Prüfungen auf der Produktionsstraße verwendet. Mit den gestiegenen Geschwindigkeits- und Qualitätsanforderungen, insbesondere in der Luft- und Raumfahrt, wurden manuelle Prüfungen verworfen. Das NORTEC 600 Wirbelstromprüfgerät von Olympus mit dem vollautomatisierten Prüfsystem von HPI bietet eine genaue, zuverlässige, zeit- und kosteneffiziente Lösung.
HPI hat für diese Lösung eine eigene Anwendungssoftware konfiguriert, die im Wesentlichen das NORTEC 600 Gerät als Sonde integriert. Das NORTEC 600 Gerät wurde von HPI speziell gegenüber anderen Wirbelstrom-Prüfgeräten ausgewählt, da das Gerät eine Schnittstelle zur Kommunikation mit einer speicherprogrammierbaren Steuerung (SPS) bietet.
Das System führt vor und nach der Leitfähigkeitsmessung automatisch Kalibrierüberprüfungen für jedes Blech durch. Aufgrund seiner Hochgeschwindigkeitskapazität werden Hunderte von Punkten, deren Messung viele Stunden dauern würde, in nur wenigen Minuten gemessen.
Der Kunde von HPI nutzt zwei dieser Systeme mit jeweils zwei NORTEC 600 Fehlerprüfgeräten. Als Qualitätskontrollprozess hat die Leitfähigkeitsqualitätsprüfung dazu beigetragen, den Wärmebehandlungsprozess von HPI zu verbessern und die Kundenzufriedenheit zu steigern.
Über das NORTEC 600 Wirbelstromprüfgerät
Das NORTEC 600 Wirbelstromprüfgerät ist ein portables Gerät mit fortschrittlicher digitaler Hochleistungsschaltung.

Einfache Integration in automatisierte Hochgeschwindigkeitssysteme
Das NORTEC 600 Gerät lässt sich einfach und nahtlos in Prüfsysteme integrieren. Es wurde entwickelt, um in industriellen Umgebungen eine beständige Leistung zu erbringen. Die Spezifikationen und Funktionen des NORTEC 600 wurden mit Blick auf Integratoren, wie HPI, entwickelt.
- Für IP66 ausgelegt
- −10 °C bis 50 °C Betriebstemperatur
- Kontinuierlicher Nullfilter
- Zeit-/Amplituden-Darstellung mit Alarm
- 6 kHz Messgeschwindigkeit
- Fernsteuerung mit der NORTEC PC Software
- Alarmausgänge
- Analogausgänge
- Digitaleingänge
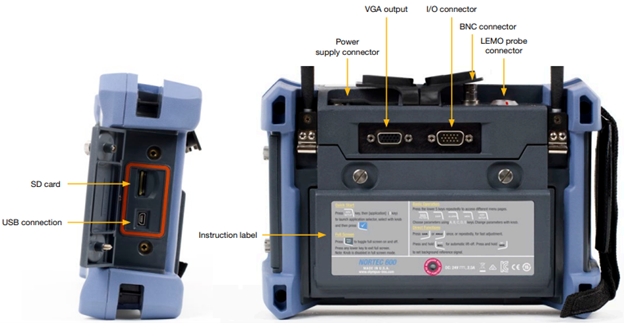
ZfP-Gerät für die Qualitätskontrolle
HPI entschied sich für die Integration des NORTEC 600 von Olympus in seine automatisierte ZfP-Lösung, da es schnelle und zuverlässige Leitfähigkeitsmessungen ohne Berührung der Materialoberfläche ermöglicht. HPI hat eine lange Geschichte als Integrationspartner von Olympus. Mehr erfahren Sie im Produktportfolio.
Ähnliche Artikel
Lösungen für die Prüfung in der Luft- und Raumfahrt
Kontakt