Introduction
Global demand for iron and steel is constantly growing, while prices for raw materials, energy, and transport continue to rise. Traditional plants require large capital budgets and incur high energy costs. The coke ovens and sintering plants in an integrated steel plant are not only expensive but have negative environmental impact due to their high carbon dioxide emissions.
Direct Reduced Iron (DRI) is a method of purifying iron ores at lower temperatures, with lower energy needs and smaller scale plants. The DRI process uses natural gas to reduce iron ore to produce a “sponge iron” product with iron concentrations (90 – 94%) similar to that of pig iron. This sponge iron is an excellent feedstock for the electric furnaces used in mini mills. DRI plants are drawing more attention as an economical and environmentally viable process to provide a stable supply source of pure iron especially with the availability of low cost shale gas.
Why is Phase Identification with XRD important?
Knowing the mineralogical composition of iron ore feedstock for DRI is critical to controlling costs and optimizing processing operations. Identifying the mineral makeup of the incoming raw materials is beneficial to the DRI processors for several reasons:
- Cost of raw materials is dependent on the grade of ore. Screening the incoming ore can help determine if the raw material is a low grade or high grade ore.
- Knowing the mineralogy of the ore helps the operators determine the optimum processing conditions such as temperature and chemical mixture to achieve the best yield and control production costs.
- Controlling the grade selection to provide consistent mineralogy allows the operators to stabilize the plant conditions.
Determination of DRI mineralogy can influence raw material costs, processing costs and the finished goods price. X-ray diffraction (XRD) can identify and quantify critical iron ore minerals such as high-grade hematite and lower-grade magnetite and goethite. It can also identify gangue minerals, including alumina, silica, gibbsite, quartz, and kaolinite which complicate processing operations.
The following diffractograms of incoming raw material from a DRI operation show the preferred phases of hematite and magnetite, all of the peaks observed are as expected for these two mineral phases.
Monitoring the process is also important to ensure that the ore has been completely reduced from its oxide form to elemental iron. An incomplete reaction will result in monetary losses through a reduction in yield. Conversely, letting the process extend longer than necessary will result in financial losses from the extra energy and fuel usage.
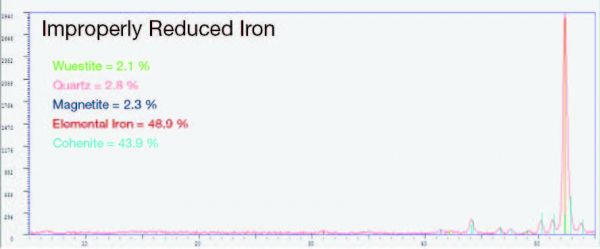
XRD identifies the different phases present. The Relative Intensity Ratio (RIR) method is used to quantify results.
X-ray diffraction analysis is a reliable method for identification of the mineralogy of an ore and the process phases. DRI plants currently utilize wet chemistry methods which are not as accurate in identifying the mineral phases. They may also send samples out to an external lab for XRD analysis which can be time consuming and costly. Olympus provides a portable XRD instruments that allow analysis to take place on site. Easy sample preparation and fast analysis time enables operators to test multiple samples to fully monitor their feedstock and process for immediate decision making in the field.
ConclusionOlympus X-ray Diffraction analyzers use patented technology developed for the NASA Mars Rover program. They provide fast, on-the-spot measurements of DRI raw materials for quality assurance and process control.
Benefits:
| ![]() TERRA Portable XRD |