Raphael Mokri at Evident France, trying out the next-gen HydroFORM scanner with the OmniScan X3 flaw detector | At Bilfinger UK’s division based in Esbjerg, Denmark, Raphael Mokri is the Advanced NDT Project Engineer. The office has around 60 employees, and Raphael’s job is to support the division in terms of any technical queries for all phased array, time-of-flight diffraction (TOFD), and other advanced NDT applications. Bilfinger is an industrial service provider specializing in asset management for the onshore and offshore energy industry. As part of their daily duties, Raphael and his team of inspection technicians regularly employ our HydroFORM™ phased array (PA) scanner with the OmniScan™ X3 flaw detector to acquire PA ultrasonic data. On a recent visit to Evident’s office in France, Raphael had a chance to try out the next-generation HydroFORM scanner and give us his feedback. Before delving into what Raphael thinks about the new design features, first we asked him to tell us a bit about the job of an NDT inspector on offshore rigs. Here is our Q&A with Raphael: | |
Your teams specialize in advanced NDT techniques such as phased array and TOFD, so what sort of services do you provide with those technologies?Raphael: Most of our clients are based either within the oil and gas industry or the wind industry. It depends on their needs, but it is mostly in-service inspection or newly fabricated inspection. This includes phased array corrosion mapping, TOFD for weld root corrosion, or more specialized applications such as touch point corrosion damage at pipe supports. Depending on the sort of service asked for, we provide a solution to the client. The main function of our NDT services is to provide our clients with some sort of reassurance that their assets can run for longer than what it was initially designed for. If you think in terms of society, ultimately, if an oil rig is running smoothly and there's no incident, then the rest of society will be running a lot better as well. We are trying to play our part by helping to prevent catastrophes such as oil spills, explosions, or collapses that could potentially cause harm to people or the environment. “Ultimately, if an oil rig is running smoothly and there's no incident, then the rest of society will be running a lot better as well.”Q: What would you say are the advantages of advanced phased array versus conventional UT?Raphael: From an in-service corrosion mapping point of view, there are two main advantages of phased array compared with conventional UT. Conventional UT is a manual, real-time inspection technique. The results are heavily reliant on the competence and reliability of the technician. Human factors play a significant role in the effectiveness of the inspections. When we apply phased array, the data is fully recordable, and therefore auditable. This brings many advantages, not only traceability and compliance with regulations, but also, and more importantly, it removes the human factors of real-time data collection, which increases the probability of detection for defects. Q: What are some of the biggest challenges you face when you're inspecting offshore?Raphael: Working offshore can be dangerous as you are secluded in the middle of the sea. The shortest flight could be about 45 minutes away. The longest one could be sometimes 3 hours away. Therefore, the safety of the personnel is one of the main challenges. Another one, and it's still very much the same, because of the remoteness, the assets we are asked to inspect cannot always be easily reached, so the use of rope access is often required. So we have to develop inspection plans that combine NDT methods with rope access. The weather is another one. We can work in very harsh weather. It can be really cold, very windy. It can be also warm depending on the country. Working in Denmark, not so much. But I've worked in Africa as well and that can be really hot. Combine that and working at heights, and we need equipment that is robust but also fit for purpose. Q: Can you tell us more about what you look for when choosing your offshore inspection equipment?Raphael: Something robust and shockproof and waterproof, because despite rain and the harsh conditions, we need to be able to work. Rain is definitely something we need to look out for, so it has to be waterproof for sure. Being able to work at night as well because we work 24/7, and so that’s another criteria. And battery life, that's also something we’re concerned about, as we can't work plugged in all the time. Shockproof is definitely an important factor, since we can’t source additional equipment in 5 minutes. Sometimes it’s days before we can get the next chopper or a week before the next boat. It is important that our equipment needs to be fit for purpose but also reliable as we make integrity decisions based on data produced by the different NDT equipment we use. Q: You already use some of our inspection solutions. Which ones and for what applications?Raphael: Mostly the OmniScan X3 device, which is the main equipment used for phased array corrosion mapping, PA weld inspection, and TOFD. In terms of probes, we use a lot of Evident probes, we use the HydroFORM and FlexoFORM™ scanners, DLA probes, DGS probes, also the A32 and A31, and the A27 DMA probe. In total, we have about 30 HydroFORM, 20 FlexoFORM, and 25 OmniScan X3 units. Separator pressure vessel on an offshore oil and gas processing platform “When we are using the HydroFORM, we're looking for internal problems, such as internal corrosion-erosion.”We use them to inspect mostly vessels. When I say vessels, I mean separation vessels. When you get fluid coming out of a well, it’s usually a mix of oil, gas, and sea water, so everything needs to be separated. It goes through a pressure vessel called a separator and, depending on the pressure and density, everything gets separated: the gas goes up via steam, the oil floats above the water, which lies at the bottom of the vessel. Depending on the sort of fluids within a pipeline or vessel, we can expect a certain sort of defect or defect mechanism. Often, we expect to see corrosion (such as pitting, microbial pitting, etc.) and erosion. When we are using the HydroFORM, we're looking for internal problems, such as internal corrosion-erosion. Our work scope is usually directed by an integrity team based onshore who make inspection plans in accordance with HOIS Recommended Practice for Non-Intrusive Inspection of Pressure Vessels – HOIS-RP-103. For a start, they might only ask to inspect the bottom half of a vessel but, depending on the results, they may extend the work to inspect the whole vessel shell to verify the extent of the corrosion found. Bilfinger’s phased array mapping composite image (top) showing the detection of corrosion and pitting in the shell of a pressure separation vessel and a photo of the vessel (bottom). A PA mapping composite image (top) and photo of the configuration (bottom) from an inspection around the bases of 3 stiffeners in a pressure vessel, detecting an inclusion and internal corrosion. Scott Westwater, Raphael’s manager, examines the warning and status lights on the ScanDeck™ module, a practical new addition to the HydroFORM scanner Q: You recently visited the Evident facility in France, and you tried the new HydroFORM scanner. How do you feel about the redesign?Raphael: Really impressed with the modifications. The probe has now 2-axis encoders which is definitely a benefit. For example, in order to assess the internal condition of piping, we capture with the HydroFORM system a succession of 50 mm wide band scans until the full required distance is inspected. One of the main challenges with the previous HydroFORM model is to keep each band scan aligned to properly capture the shape of the corrosion. Since the new HydroFORM scanner has now 2 encoders to record both in the scan and the index axes, we are now able to get more reliable data. We can easily capture the proper shape of the corrosion, which will ultimately help the integrity team make accurate fitness-for-service calculations determining how long we can keep the assets running. “We can easily capture the proper shape of the corrosion, which will ultimately help the integrity team make accurate fitness-for-service calculations determining how long we can keep the assets running.”Another feature was the fact we didn't need as much water as coupling, the new probe retains the water a lot better compared to the older version. When you're working in conjunction with rope access, for instance, we don’t always have access to a continuous water feed, so we usually work with manual water pumps that need to be refilled every so often. If the probe uses less water, then the work is more efficient as it can be achieved quicker. This is a definite advantage since working on ropes can be difficult and physically demanding.
Q: What kind of problems can these new features help ease or solve?Raphael: All the indicator lights will help in terms of efficiency. Instead of finishing your scan and then realizing it might not be as good as it should be, the scanning assistant can now realize by themselves when they are going too fast rather than being instructed by the OmniScan X3 operator. This is definitely an advantage since we are usually working in a noisy environment and communication can be challenging. All these new features will help a lot, both in terms of data collection but also for the data analysis side. They will certainly help us to improve the quality and the reliability of our scans. If we have more reliable data, that’s for sure going to help our clients. “If we have more reliable data, that's for sure going to help our clients.”To learn more about the improved HydroFORM scanner, go to www.olympus-ims.com/corrosion-solutions/hydroform Related ContentCornering the Pipe Elbow Inspection Market with the FlexoFORM™ Scanner First, We Simplified Long Seam Inspection and Now, Circumferential Weld Scanning Master Pipe Weld Scanning with This Versatile Tool Get In Touch |
A Day in the Life of an Offshore Inspector and the HydroFORM™ Phased Array Scanner
By 27 June, 2023
-
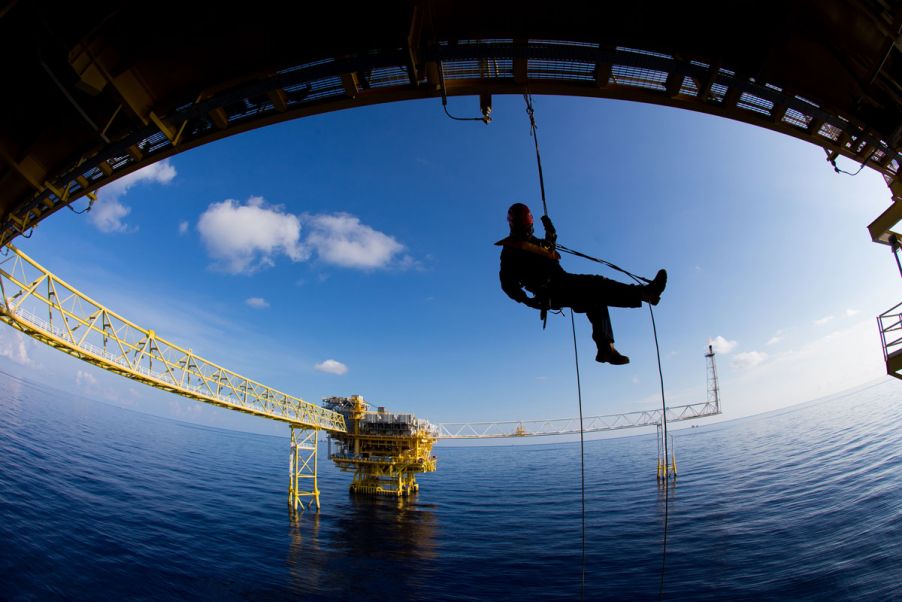