The Problem
Certain critical wind turbine components are highly susceptible to fretting corrosion, which can contribute to functional failure. The expected life of wind turbines is around 20 years, and manufacturer warranties usually only cover the first 2 to 5 years of operation, so owners and operators need reliable corrosion analysis tools to support their warranty claims. X-ray diffraction (XRD) is currently used to positively identify and quantify fretting corrosion using wear debris samples. But traditional X-ray diffraction laboratory analysis requires bulky, cost-prohibitive equipment, large sample sizes, and the work itself is very costly— typically $750 per sample—with turnaround times measured in weeks.
The illustration below identifies some of the places where fretting is commonly found in wind turbines, depending on the model.
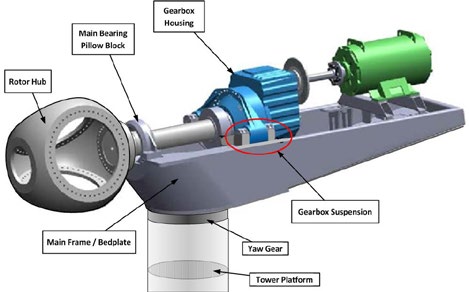
Image used with permission from Wind Driven LLC.
For example, in the rotor hub, fretting corrosion has been observed in pitch linkages, pitch gears, and blade bearings.
Wind turbines have increased rapidly in both size and number in the last decade. As their size has increased, scaling effects have resulted in new, previously unseen failure modes. Axial cracking of the inner rings of high-speed gearbox bearings is the most widely known of these new scaling-related failure modes; fretting corrosion is another example. It is a mechanically, rather than chemically, driven corrosive wear process, but it is no less destructive, and yet it remains virtually unknown to the wind industry.
Fretting corrosion in wind turbines occurs between two steel surfaces that come into contact under pressure and are subjected to minute vibratory motion. It occurs in both lubricated contact and dry contact, but dry contact fretting is typically more destructive. In lubricated components, it occurs in two steps; the first produces black iron oxide magnetite, which creates a dam around the contact zone, blocking the inflow of lubricants. The second stage produces red iron oxide hematite, which is a very hard, fine-grained abrasive that is most commonly used to polish gems. Magnetite and hematite are hard crystals with sharp edges and corners that provoke abrasive wear. The top images below show (1) a close-up view of fretting wear debris and (2) an overall view of the consequences of fretting on a gearbox shaft key. The bottom images show pitch gear and gearbox housing fretting; both are lubricated systems.
![]() Hematite wear debris emerging from the interface between the main bearing housing and a bedplate. | ![]() Severe fretting corrosion and material removal of a WT gearbox key, which caused shaft cracking. |
![]() Initiation phase of fretting corrosion of manually lubricated pitch gears. Eight years later, these gear teeth are nearing functional failure. | ![]() Gearbox housing fretting corrosion at a split line. In this example, reddish hematite is clearly visible. |
All images used with permission from Wind Driven LLC
Relative to other industrial applications, wind turbines are subject to intense load variations. On top of this, as the size of wind turbines increases, because of scaling effects, component weight has increased twice as fast as the surface areas in contact zones, such as bolted connections. This is known as a “surface area to volume ratio” problem. With greater mass and a smaller contact area, fretting has been found in critical components and interfaces where it was not found in the past. Also, safety factors have been reduced to cut costs and weight. There is a strong market incentive for minimizing nacelle and rotor weight to lower the costs of towers and foundations.
The Solution
Field and lab investigations of wind turbine wear debris samples, both dry and mixed with a lubricant, were performed with the Olympus TERRA® portable XRD analyzer. These trials successfully and quickly identified and quantified fretting corrosion debris, demonstrating that turbine owners, wind industry service providers, and sample analysis labs can benefit from using the TERRA or BTX II™ XRD analyzers, especially in pursuing warranty issues. The field investigation required few tools and supplies beyond the TERRA unit itself, as shown in the photo below. Data from the fieldwork are summarized in the table below. As the ratio of hematite to magnetite increases, the alpha iron (Fe) begins to show up in the most worn parts. The Olympus TERRA XRD analyzer was more than capable of detecting all three of the individual constituents in the lubricated samples— magnetite, hematite, and alpha iron. |
Doc WT Number | Description | Hematite | Magnetite | Alpha Iron |
WT-1 | Main Link 2 | 55% | 30% | 15% |
WT-1 | Main Link 3 | 60% | 37% | |
WT-2 | Main Link 1 | 55% | 46% | |
WT-2 | Main Link 2 | 57% | 40% | |
WT-2 | Main Link 3 | 53% | 30% | 17% |
WT-3 | Intermediate Linkage | 57% | 36% | 7% |
WT-4 | Intermediate Linkage | 48% | 33% | 19% |
WT-4 | Main Link 1 | 56% | 44% | |
WT-4 | Main Link 2 | 59% | 38% | |
WT-4 | Main Link 3 | 60% | 40% | |
WT-5 | Main Link 1 | 35% | 60% | |
WT-6 | Main Link 2 | 61% | 39% | |
WT-7 | Link Arm | 51% | 38% | 11% |
WT-8 | Main Link | 54% | 46% | |
WT-9 | Gearbox Torque Arm Blocks | 61% | 39% | |
WT-10 | Intermediate Linkage | 52% | 33% | 15% |
WT-10 | Main Link 1 | 43% | 57% | |
WT-10 | Main Link 2 | 41% | 59% | |
WT-11 | Main Link | 47% | 53% | |
WT-12 | Main Link | 65% | 35% | |
WT-13 | Intermediate Linkage | 57% | 25% | 18% |
WT-14 | Gearbox Torque Arm Blocks | 48% | 52% | |
WT-15 | Intermediate Linkage | 50% | 50% | |
WT-16 | Intermediate Linkage | 36% | 22% | 43% |
WT-17 | Intermediate Linkage | 45% | 31% | 23% |
WT-18 | Main Link | 58% | 38% | |
WT-19 | Main Link | 45% | 52% | |
WT-20 | Intermediate Linkage | 51% | 37% | 12% |
X-ray diffraction (XRD) is a commonly used technique for corrosion analysis and works well in this application. Additionally, both the TERRA and BTX II analyzers give qualitative X-ray fluorescence (XRF) data on the elemental composition of the samples. This is useful in determining the source of fretting wear debris. For example, using XRF, it was determined that fretting wear was occurring in spherical bearings in the pitch linkage. The graphic scans show the sensitivity of the samples with good peak-to-background ratios, as is evident from the representative XRD patterns shown below. |
Conclusions
The Olympus TERRA portable XRD analyzer and the BTX II benchtop XRD spectrometer are ideal for quickly and economically identifying and quantifying fretting corrosion in the wind energy industry. The microcrystalline iron oxides, which form as a result of corrosion, are abrasive. This fretting corrosion shortens the lifespan of wind turbine equipment, undermines investment, and can even pose safety risks. Olympus XRD instruments provide an analytical solution for detecting and responding to fretting corrosion. The XRF feature provides additional qualitative data on the elements found in the samples. Elemental signatures can assist in identifying the failing components. Both can provide you with superior resolution for separating phases.
Fretting corrosion will inevitably cause problems with wind turbine component interfaces using bolted connections and open gears. The resulting looseness strongly influences the longevity and repair costs of pitch systems, main bearings, gearboxes, yaw drives, and other affected components both large and small.
Wind turbine owners and operators may remain unaware of the destructive power of fretting corrosion until failure has occurred. Proactive early detection, especially during the warranty period, is greatly enhanced through modern Olympus XRD instruments. Many wind turbine asset-owners already have inspection and preventative maintenance programs in place. Since the TERRA XRD analyzer is portable and field-ruggedized, it can be a useful maintenance program tool. Olympus’s XRD technology has an instrumental role to play in maintaining the investment of wind turbine owners.
Recommendations
All wind turbine warranty sweeps should include inspections for fretting corrosion. If found, samples should be collected, analyzed by XRD, and included in warranty claims.
Corrective actions for fretting include increasing fastener preload, improving surface finishes, the addition of friction shims, such as those embedded with diamond powder, improving lubrication in open gears, reducing vibrations and fault rates, and avoiding long periods with the high-speed brake applied.