Bo Hyun Kim先生は、韓国の崇実大学School of Mechanical Engineeringの教授です。デジタルマイクロスコープと3D共焦点レーザー顕微鏡を使用して、超精密微細加工技術を研究しています。今回は研究の詳細と、有意義な成果を得るために使用した顕微鏡についてお話を伺いました。
Q:超精密微細加工技術について教えていただけますか?
Bo Hyun Kim教授:超精密微細加工技術とは、マイクロメートルサイズの形状や部品を、ナノメートルレベルの精度と粗さで加工する製造技術です。超精密微細加工技術へのニーズは、情報技術、電子部品、マイクロメカニカル部品や金型などの分野で急速に高まっています。また、応用分野もさらに広がっています。
こうした技術的な要請に応えるため、Precision Engineering and Manufacturing Laboratory(PREMA)では、微細加工、ドリル加工、研削などの超精密加工技術や放電加工(EDM)、電解加工(ECM)の研究を行っています。
代表的なな研究分野としては、以下のようなものがあります。
- 高硬度材料(セラミックス、超硬合金、サファイアガラスなど)の超精密加工
- マイクロ放電加工(マイクロEDM)
- マイクロ工具製造技術
- ハイブリッド加工技術(切削、研削、EDM、ECM、レーザー加工などの加工技術を組み合わせたもの)
Q:この分野の研究で得られた成果と、その成果を得るために使用した機器について教えてください。
Bo Hyun Kim教授:私の研究では、さまざまな方法で加工面を観察・測定することがとても重要です。
さまざまな加工パラメーターが精密加工に影響を与える場合があります。そのため、各工程で加工が正しく行われているか、画像のチェックや加工面の測定を継続的に行う必要があります。
例として、延性モードで加工されたPyrexガラスの表面を取り上げてみましょう。
下の最初の画像(図1左)は、マイクロ多結晶ダイヤモンド(PCD)工具を使用してPyrexガラス表面に加工した微細溝を示しています。ガラス材は非常に脆いいため、ガラスにクラックのないごく小さな形状を加工することは困難です。例えば、画像の縦の溝は1 µmの切削深さで加工されています。切削深さが1 µmであっても、ガラス表面にたくさんのクラックが残っています。ただし、切削深さを水平方向の溝で0.25 µmにすると、ガラスにクラックが入ることなく加工でき、これを延性モード切削と呼びます。
PCD工具の耐久性を高めるため、あるいは加工時に頻発するクラックの原因を取り除くには、実験条件を変えながら粗さや表面の変化を確認することが重要です。
この場合、加工面の観察と測定には、デジタルマイクロスコープと共焦点レーザー顕微鏡が有効です。EvidentのDSX1000デジタルマイクロスコープとLEXT™ OLS5100 3D共焦点レーザー顕微鏡を使用して、表面の観察と測定を行うことで、延性モードでクラックのない表面を作るために加工品質を向上させることができました。
これら顕微鏡による成果をご紹介します。
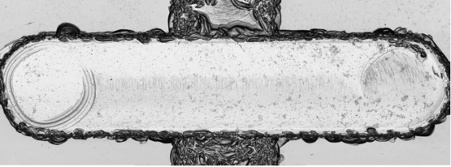
図2:Pyrexガラス表面に加工された微細溝拡大画像は、切削深さが0.25 µmの場合、Pyrexガラスをクラックなく加工できることを示しています。これを延性モード切削と呼んでいます。画像取得と測定には、OLS5100 3D共焦点レーザー顕微鏡を使用しています。
送り速度(µm/秒) | 切削深さ(µm) | 合計深さ(µm) | |
---|---|---|---|
脆性モード | 100 | 1 | 10 |
延性モード | 20 | 0.25 | 14 |
研削加工条件 | |
---|---|
使用工具 | PCD |
粒度(µm) | 10 |
工具径(µm) | 150 |
作動静電容量(pF) | 500 |
対象材料 | Pyrex |
回転速度(rpm) | 60,000 |
送り速度(µm/秒) | 20–100 |
切削深さ(µm) | 0.25–1 |
合計深さ(µm) | 14 |
- 条件(1)で脆性表面を形成した後、条件(2)で交差による延性モード加工を施す
- 脆性クラック(段差:4 µm)より深く加工しながら、クラックのない延性モード表面を形成する
送り速度(FR):µm/秒 | 切削深さ(DOC):µm | 合計深さ:µm | 平均表面粗さ(Ra):µm | 最大高さ(Rz):µm | |
---|---|---|---|---|---|
1. 脆性 | 100 | 1 | 10 | 0.437 | 2.589 |
2. 延性 | 20 | 0.25 | 14 | 0.015 | 0.141 |
図3:脆性モードと延性モードで加工されたガラスの表面粗さの比較使用機器:OLS5100 3Dレーザー走査型顕微鏡
デジタルマイクロスコープと3D共焦点レーザー顕微鏡を使い、粗さ解析データと加工精度を比較し、加工パラメーターの決定に反映させれば、加工品質を大幅に向上させることができます。これは、より高品質な加工が製品の品質向上につながるという意味で重要なことです。
Q:今後の研究計画を教えてください。
Bo Hyun Kim教授:今後もPrecision Engineering and Manufacturing Laboratoryは、さまざまな分野の超精密加工に関する有意義な学術的・実践的研究を進めていきます。
超精密微細加工技術に関する参考文献
超精密微細加工技術に関する詳細は、Bo Hyun Kim教授による以下の論文をご覧ください。
- Applied Sciences | Free Full-Text | Experimental Study on Micro-Grinding of Ceramics for Micro-Structuring (mdpi.com)
- Micromachines | Free Full-Text | Microfluidic Chip Fabrication of Fused Silica Using Microgrinding (mdpi.com)
インタビュー対象者のご紹介
![]() | Bo Hyun Kim先生は、韓国の崇実大学School of Mechanical Engineeringの教授であり、硬質材料の超精密加工分野のエキスパートです。 放電加工、電気化学加工、レーザー加工などの超精密微細加工技術や、切削、フライス、研削などの機械加工に関する先端研究、論文発表を通じて学術に貢献しています。 |