L’analyse du nombre et de la nature des contaminants (particules, poussières et résidus) à la surface des composants ou dans les fluides est essentielle au bon fonctionnement et à la sécurité des produits dans de nombreux domaines d’application du secteur de la fabrication. Des secteurs industriels comme l’automobile, l’aérospatiale et la fabrication de dispositifs médicaux ont des normes et des méthodes spécifiques à suivre pour évaluer la propreté des composants.
La première étape du contrôle et de l’analyse de la propreté est le prélèvement d’un échantillon de composant. La méthode d’échantillonnage spécifique utilisée dépend de l’industrie et du domaine d’application. Dans un article précédent, nous avons décrit le processus d’échantillonnage général et les méthodes d’échantillonnage utilisés lors des contrôles de la propreté des composants.
À présent, notre série d’articles de blogue détaillera chaque méthode d’échantillonnage, en commençant par la méthode de lavage.
Qu’est-ce que la méthode de lavage utilisée lors des contrôles de la propreté des composants ?
La propreté des composants est analysée indirectement, car les produits examinés ne sont pas inspectés directement au microscope. Les microparticules contaminantes sont éliminées des composants par lavage et par rinçage, ou dans un bain à ultrasons. Avec la méthode de lavage, les résidus et les particules sont extraits du composant et demeurent ensuite dans le liquide de rinçage.
Remarque : Dans la plupart des cas du secteur automobile, l’extraction de particules au moyen d’un liquide est une technique appropriée. Assurez-vous que le liquide utilisé pour l’extraction est compatible avec le matériau du composant, le dispositif de filtration et la membrane filtrante.
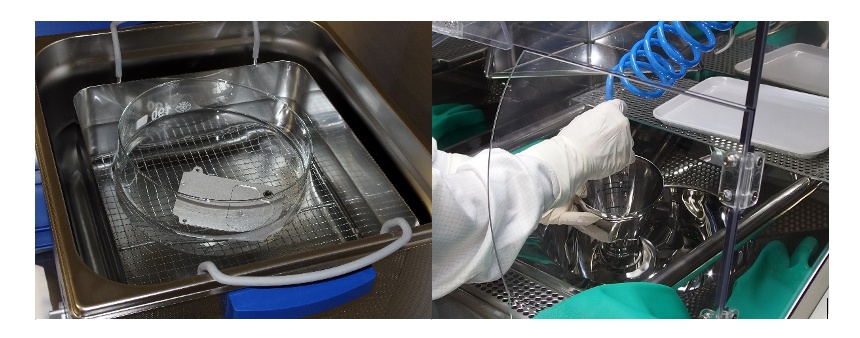
Dans le cadre d’un contrôle de propreté, les particules sont extraites des composants par lavage. Les images montrent des exemples
d’utilisation d’un bain à ultrasons (à gauche) et de lavage d’une pièce dans une armoire d’extraction (à droite).
Après extraction, le liquide de rinçage est filtré afin que les particules se déposent sur une membrane filtrante. Le filtre doit ensuite être séché pour poursuivre l’analyse. Le liquide de rinçage ou l’huile peuvent être éliminés dans un dessiccateur ou un four de séchage, ou au moyen d’un autre type d’équipement prévu à cet effet.

Séchage d’un filtre pour le préparer pour un contrôle de propreté
Parfois, l’étape suivante consiste à peser la membrane filtrante séchée à l’aide d’une balance de précision avec cage vitrée intégrée. Une comparaison de son poids avec et sans contaminants donne une première estimation approximative de l’ampleur de la contamination des pièces sélectionnées. Toutefois, ces données gravimétriques sont facultatives et ne fournissent pas d’informations sur la taille, la forme et les autres propriétés des particules.

Une membrane filtrante est placée sur une balance avec cage vitrée intégrée.
Une analyse plus approfondie effectuée avec un système de microscopie fournit des informations détaillées sur le nombre, la distribution granulométrique et les caractéristiques des particules pour permettre la vérification de la conformité aux normes de propreté des composants. Pour effectuer l’analyse visuelle, un opérateur fixe la membrane filtrante sur le porte-échantillon, puis installe celui-ici sur la platine du microscope pour l’acquisition et l’analyse des images.

Une membrane filtrante est installée sur un porte-échantillon.
Pour l’analyse visuelle, nous recommandons l’utilisation d’un système de microscope automatisé avec guidage pas à pas au cours du processus d’analyse afin que les utilisateurs de tous niveaux puissent obtenir des données fiables à partir des images obtenues. Apprenez-en plus en lisant notre article intitulé Sept fonctionnalités qui facilitent les contrôles de la propreté des composants pour les utilisateurs débutants.
Types de membranes filtrantes utilisées pour la méthode de lavage
Les membranes filtrantes sont disponibles en différents diamètres. Notre système de contrôle de la propreté OLYMPUS CIX100 utilise par défaut une membrane filtrante de 47 mm de diamètre. Des porte-échantillons sont disponibles pour des membranes de 47 mm, 25 mm et 55 mm de diamètre.
Le logiciel du système inclut désormais des préréglages de zone d’inspection adaptés aux différentes tailles de membrane, ce qui permet aux utilisateurs d’ajuster automatiquement et en un clic la taille de la zone d’analyse. Le logiciel comprend également des paramètres prédéfinis pour chaque type d’échantillon afin que même les opérateurs inexpérimentés puissent facilement obtenir des résultats.
La taille de la membrane filtrante utilisée dépend du domaine d’application et de l’industrie :
- Les membranes filtrantes de 47 mm de diamètre sont souvent utilisées dans les industries aérospatiale, automobile et pétrolière. Il s’agit du diamètre de filtre par défaut utilisé dans la plupart des cas.
- Des membranes de 25 mm de diamètre sont parfois utilisées pour les analyses d’huiles.
- Les membranes filtrantes de 55 mm de diamètre sont utilisées dans la maintenance des machines et dans la production impliquant un grand volume de particules.

Porte-échantillons circulaires à fond blanc et fond noir pour membranes filtrantes
d’un diamètre de 25 mm (à gauche), de 47 mm (au centre) et de 55 mm (à droite)
En plus des différents diamètres disponibles, nos porte-échantillons sont disponibles avec fond noir et fond blanc pour s’adapter à différents types d’analyses et d’échantillons. Voici quelques exemples d’utilisation des différents fonds de porte-échantillon :
Fonds noirs : Si un produit chimique agressif est utilisé pour rincer les particules, certains résidus du liquide de rinçage peuvent rester sur la membrane du filtre. Le porte-échantillon à fond noir se compose principalement d’aluminium anodisé, ce qui le rend hautement inerte aux substances chimiques (c’est-à-dire qu’il ne réagit pas chimiquement). C’est notamment un avantage lors d’analyses d’huiles, car l’huile est souvent diluée avec du pétrole propre pour permettre un meilleur filtrage sur des membranes de cellulose. Les résidus de solvant sur les membranes filtrantes pourraient détruire le fond blanc du porte-échantillon.
Fonds blancs : Les fonds blancs sont utiles lors de l’utilisation de filtres à mailles tissées. Ces filtres sont souvent utilisés pour accélérer le processus de filtrage, car le liquide de rinçage peut s’écouler beaucoup plus rapidement à travers la membrane filtrante. Lors de l’examen d’un filtre à mailles, le microscope permet à l’utilisateur de regarder à travers les mailles sur le porte-échantillon. Sur un fond noir, des points noirs apparaîtraient à travers le motif de tissage et seraient interprétés à tort comme des particules. Pour cette raison, l’utilisation d’un porte-échantillon à un fond blanc est recommandée lors de l’examen de filtres à mailles.
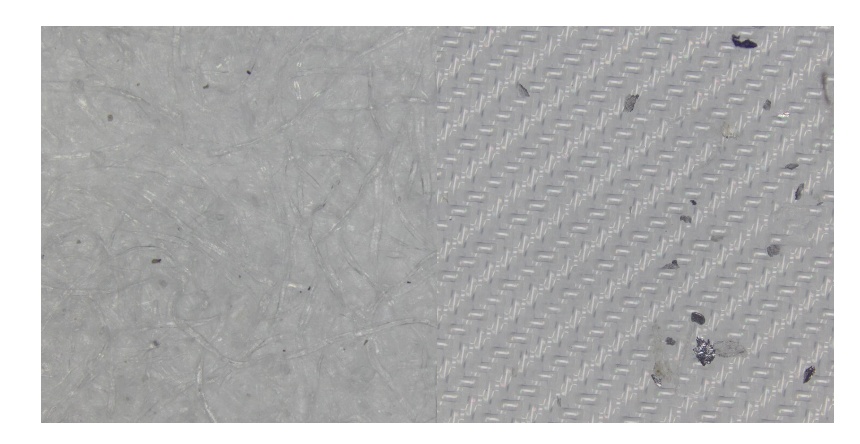
Images de membranes filtrantes sur fond blanc. La membrane filtrante à mailles (à droite) a un motif de tissage
distinct, tandis que la membrane filtrante en cellulose (à gauche) ne laisse pas transparaître le fond du filtre.
Découvrez les autres techniques d’échantillonnage utilisées dans les contrôles de propreté
Nous publierons prochainement d’autres articles sur les techniques d’échantillonnage utilisées dans les contrôles de la propreté des composants. Dans notre prochain article, nous aborderons la filtration directe de liquides. Pour rester informés et consulter d’autres articles utiles sur les contrôles de propreté, abonnez-vous au blogue InSight dès aujourd’hui. Vous pouvez également consulter notre brochure sur les principes fondamentaux du contrôle de la propreté des composants pour en savoir plus sur le processus de contrôle standard.
Contenu connexe
Une image vaut mille mots lors des contrôles de la propreté des composants