Background:
The dipper handle is a critical component of many shovels and draglines involved in excavation at surface mines. This component allows for the raising and lowering of the dipper basket in conjunction with the boom. A failed dipper handle can cause safety issues as well as loss of profit based on overall machine down time. Therefore, efficient inspection and repair of these components is critical.
Box type dipper handles are typically rectangular and contain bulk head supports that are internally fillet welded for strength reinforcement to the dipper handle. Unfortunately, this design creates a geometry that can be difficult to inspect and repair if cracks in the weld or side walls are found. Crack repair often necessitates cutting a window into the side frame to allow access to the defect.
A fast and accurate inspection is very important, because the repair process can be involved and time consuming. A fillet/T weld is recommended to be inspected from at least two surfaces. Unfortunately that’s not possible with dipper handles since the entire area, except one surface, is enclosed. Cracks often occur at the toe of the fillet weld and can move into the sidewall.
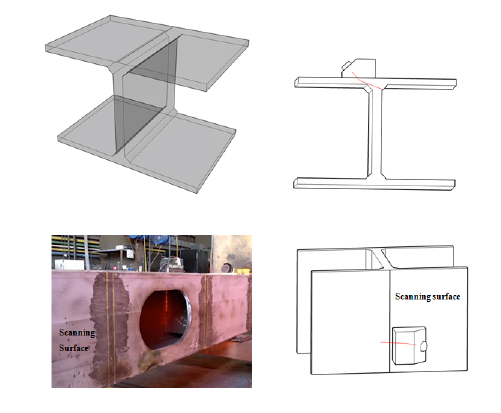
Schematic of fillet weld in Dipper Handle. Note access window cut out for repair of weld cracks.
The Solution: Phased Array vs. Conventional Ultrasound
With a manual phased array flaw detector, inspection of the weld is initiated by rastering the probe in and out of the weld area and down the weld. The advantage of using a phased array detector is derived from the multiple angles that are available and the image shown on the phased array units.
![]() | ![]() |
On the other hand, with a flaw detector using conventional ultrasound it is difficult to decipher the geometry of the weld versus cracks in the weld or side walls. Conventional flaw detectors can only image a single angle off a fillet weld at a time. Furthermore, they are only sensitive to cracks that are perpendicular to the set angle. Multiple probes of varying angles can increase the probability of crack detection or other flaw, but that approach is very time consuming.
Summary: Advantages of the Phased Array Method
- Time Savings, 50% or more due to less pull back scan distance and faster defect assessment and one probe versus multiple probes of varying angles
- Increased probability of detection due to multiple angles
- Less false calls due to geometry with aid of imaging
- Data files of indications (S-scans) can be saved with all raw data for aid in reviewing and discussing indications for proper disposition
Equipment Used
- OmniScan or EPOCH Phased Array Flaw detector (EPOCH 1000i or OmniScan SX most common)
- 16 element or greater phased array probe
- Shear wave phased array wedge
- Couplant
Final comment:
Dipper handles can be an important but challenging inspection for conventional ultrasound due to access, geometry of the weld and inherent limitations of the conventional method. But when the inspection is performed with a phased array flaw detector, the operator gains from time savings as well as from better and more accurate detection and assesment rates.
For a customer testimonial on the subject please visit the video section of the website.